Instrumentation (optics and sensors) and other equipment (mechanical parts, PCBs, mechanisms) to be placed in vacuum – either in on-ground test facilities or during flight in space - often require ‘bakeout’ prior to vacuum exposure in order to remove potential contaminants such as hydrocarbons and water which could adversely affect the instrument under test or the environment (vacuum test chamber, spacecraft platform). The UL Vacuum Bakeout Chamber (VBC) is sited within a clean (ISO 6), AIV area in the SRC, adjoining and with direct access to the large cleanroom, permitting appropriate handling of contamination-sensitive equipment. The chamber has a capacity of ~0.6 m3 (0.8 m diam x 1.2 m length), and is equipped with two jacket heaters, a rotary-pump-backed turbo-molecular pump, a Faraday mass spectrometer for residual gas analysis (RGA), a Temperature-controlled Quartz Crystal Microbalance (TQCM), vacuum gauges, feedthroughs for temperature-control instrumentation and a gaseous nitrogen back-fill system for clean return to ambient pressure. The heater system can achieve a maximum chamber temperature of +125°C, and uses feedback from two PRTs to control the temperature of the baked items. A further ‘watchdog’ PRT is linked to a separate automatic heater shutdown to provide additional protection against exceeding temperature limits. The VBC has been used to date for bakeout to ESA/NASA standards, for several astrophysics and planetary space missions, including cases with sensitive optical surfaces, instances where the temperature limit had to be closely monitored and safeguarded, and contracted work for international partner organisations in Europe.
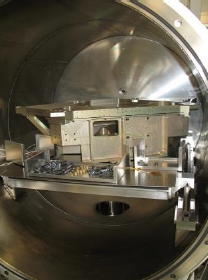
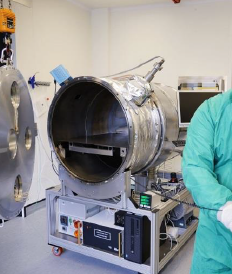